コミュニケーションが最大の成果を生むフィジカルフェーズ
デジタルフェーズが完了すると、いよいよ実車でのモノづくりとなるフィジカルフェーズが始まる。正規型を使った部品による試作から始まり、その性能・品質確認のための各種ロット、そして量産品質確認のための最終ロットという流れだ。デジタルフェーズで様々な検証はしているものの、実際につくってみないと分からない部分を確認・実証して行くのがフィジカルフェーズの役割である。各ロットには具体的なクリアすべき目標-KPIが設定されている。性能や品質の検証はもちろん、実際の生産方法の確認・調整も含めて、リアルタイムで問題を修正し、KPIをクリアしていくのだ。
今回の新プロセスにおいて、開発のフィジカルフェーズが驚くほどうまく行ったのは、「同じ屋根の下に集った両社のメンバーの良好なコミュニケーションのおかげ」と齊藤CVE(Chief Vehicle Engineer)はいう。軽自動車の開発経験のなかった日産自動車は、例えば、部品ひとつとっても乗用車より小さいといった課題がある。それ以外にも様々な課題があり、その解決には軽のエキスパートである三菱自動車の設計者との連携が必要であった。両社のメンバーがNMKVという傘の下に集まり、企業間の壁を越えた密なコミュニケーションによって克服してきたのである。
もちろん、結果を出すまでのプロセスは簡単ではなかった。両社ではそれぞれの組織や工程が違うため全体を通して工程をつないでいくと、どうしても抜け漏れが発生する。例えば、「日産自動車設計で日産自動車購買の部品は水島製作所が発注する」などの約束事を、ひとつひとつ決めて行った。十何種類あるそういった組み合わせについて、カテゴリーを分けて購入するところから始めた。その結果、最初の定置艤装で出来上がった試作車には、欠品が皆無だったという。これは、過去の経験から見ても極めて優れた成果だった。
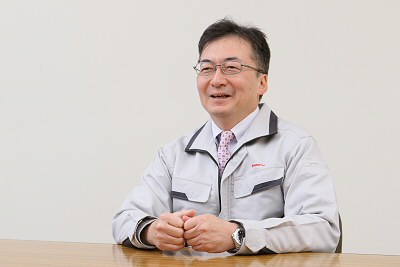
齊藤CVE
「ゴールはお客様。良いクルマをつくることができれば、きっとお客様に喜んで頂ける。そう信じているからこそ、クルマづくりに邁進できるのです。そして、つくったクルマが高く評価されたという喜びに勝るものはありませんし、次期車をそういうクルマに仕上げる自信はあります」と齊藤CVEは語気を強める。デザインでは両社それぞれの“らしさ”を表現できた、ハードウェアはライバル車と戦える仕様になっている。あとはきちんと仕上げ、お客様の期待に応えるだけである。