インサイト化活動
前回に続き、生産現場でのコスト改善活動についてご紹介します。テーマは「インサイト化活動」です。NMKVのバイスプレジデントであり三菱自動車水島製作所副所長も務める野村泰弘、そして三菱自動車から高田直樹、林浩の3名に話を聞きました。

▲写真左から/高田、野村、林
生産体制再構築プロジェクトの流れを汲むインサイト化の取り組み
- 耳慣れない言葉ですが、そもそもインサイト化とはどういう取り組みなのでしょうか。
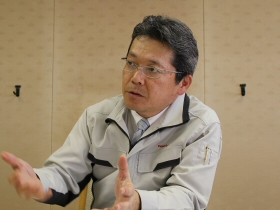
野村:そうでしょうね。私たちもこの取り組みから使い始めた言葉ですし、おそらく、一般にもあまりなじみのない言葉だと思います。インサイトとは、サプライヤー様が、自社の敷地ではなく、取引先メーカーの工場敷地の中で部品を製造することを意味しています。ただし、経営の主体はあくまでもサプライヤー様で、メーカーは場所だけを提供します。ちなみに、部品を自社で内製するのがいわゆるインハウス、サプライヤー様が車体ラインと同じ建屋内で製造することをオンサイト、同じ敷地内で製造することをインサイトと呼んでいます。
インサイト化は、部品をサプライヤー様から輸送する際の物流費を抑止できますし、仕掛かり在庫も減らせる強力なコスト削減の手法であり、輸送時の変形、キズ、汚れなどのリスクを低減し、品質向上も図れます。
- なるほど。このような取り組みは以前からあったのですか?
野村:日産自動車との協業以前から水島製作所では生産体制再構築プロジェクトを進めてきました。これは、実際の生産能力や生産台数を勘案して、現状に見合った生産ラインを再構築していく作業です。
高田:例えば複数ある溶接のラインを見直して、ライン数を減らして規模を適正化し、そのライン跡地スペースを活用して部品の自社内製化を進める構想をもっていました。ところが、ちょうどその頃、日産自動車との協業が始まって、NMKVを通じて、日産自動車からインサイト化という取り組みが紹介されました。言うまでもなく、サプライヤー様の作る部品にはさまざまなノウハウが活かされています。これを自社で一から内製化するよりは、サプライヤー様に水島製作所の敷地に入っていただき同じ敷地の中で物流コストをミニマムにして部品を製造していただく方が、より現実的で物作りとしても理想の形ではないかと考え、そこから5社のサプライヤー様を対象にインサイト化の取り組みを始めたわけです。
林:インサイト化は、三菱自動車としては初めての取り組みですが、これまでの生産体制再構築の考え方と日産自動車の経験・アイデアをプラスして、新しいスキームを作ることができました。
NMKVのリードで最速かつ最適にインサイト化を実現
野村:日産自動車からは、オン/インサイトという考え方だけでなく、具体的にオン/インサイト推奨部品リストまで提供していただきました。三菱自動車の水島製作所では、これまでの生産体制の再構築の取り組みを加速することでそれに応えました。
- まさに理想的な協業体制ですね。
野村:そのとおりです。でも、これにはやはりNMKVの存在が大きいです。普通なら、コストダウンのキモになるノウハウなど、トップシークレットです。おいそれとは出てくるものではありません。NMKVが間に入ることではじめて、お互いに、従来なかったノウハウ・経験を共有することができたのです。結果、水島製作所は、より安価で高品質な軽自動車を作るのにふさわしい筋肉質で高効率な工場に生まれ変わりつつあります。
- なるほど。ここでもNMKVのいいとこどりの価値創造力が活きているのですね。皆さんはこの取り組みにそれぞれどのようなポジションで関わられているのでしょうか。
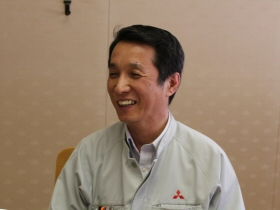
林:水島製作所の生産体制再構築プロジェクトは、野村副所長が推進の総責任者です。それを、高田さんと私のコンビで一緒に推進しました。
高田:私たちは、もともと生産体制再構築プロジェクトのメンバーで、その流れの中でインサイト化の実行計画検討、実行調整、進捗確認等を行いました。
野村:私はNMKVの社員の立場で、日産自動車やNMKVの担当からの情報やノウハウの調整・集約を行う一方で、水島製作所副所長として、高田や林とともに、計画のチェックやフォローなど、実行フェーズの全体を推進しています。
生産を止めずに設備を移設する緊迫のプロジェクト
- 皆さんがインサイト化の中心なのですね。実際にインサイト化を進めるにはご苦労はありましたか。
野村:まず、インサイトに協力いただけるサプライヤー様探しから大変でしたね。そもそも「インサイトって何」というところからの説明です。「内製化するってことですか?私たちの仕事はなくなるんですか?」という反応ですから、「いえいえ、そうではありません。場所をお貸しするということです。サプライヤーさんの設備を水島製作所に運んでいただいて、そこで部品を製造していただくのです」と丁寧にご説明しました。
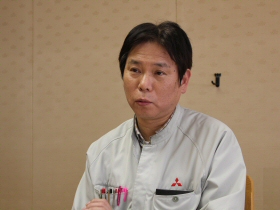
高田:私は調達部門と一緒に、サプライヤー様と折衝しました。本来望ましいのは、新しい車用の部品生産ラインを作るときにインサイト化のご相談も一緒にすることなんですが、今回は、既に現行のデイズ/eKワゴン、デイズルークス/eKスペース用のライン稼動後であるので既存ラインを移設する必要があり、移設コストも障害でした。ただ、自社のノウハウを保持しつつ物流コストを効率化できるというインサイトのプラスの面をご理解いただいたサプライヤー様からは、積極的に協力していただけたので、無事乗り越えることができました。
林:そして、やはり一番大変だったのは、実際の移設作業です。私たちにとって生産計画の維持と品質は生命線です。インサイト化による移設工事での品質トラブルでのライン停止は絶対に避けなければなりません。ですからインサイト化が可能な日程はお盆休みと年末年始の大型連休だけ。年末年始に移設した溶組ラインは工事ボリューム多く、移管後の品質確認に日程を要する移設工事でしたが、サプライヤー様と私たちで昼夜ツーシフトの24時間体制で設備移管、品質玉成に取り組んで、無事、休み明けには通常通り生産を開始することができました。
- 実は大変な苦労あってのインサイト化なのですね。驚きました。この取り組みの現時点での成果を教えていただけますか。
林:今回は、既にサプライヤー様で生産稼動しているため大物部品で、荷姿が悪く、物流コストが高く、移設コストを上回るインサイトメリットのある5社の溶接組立、ガラス組立、床下配管曲げ加工部品が対象になりました。ボンネットとかドアなどの溶接組立部品は、今まで外板部品を水島製作所でプレスし、サプライヤー様まで運んで溶組Assyし、また水島製作所に運んでくるという逆物流となっていましたが、インサイト化により物流の無駄排除と外板部品の品質向上が図れました。今後車種が替わっても活きてくる重要な改善ができたと思っています。
まだまだ続くインサイト化の取り組み
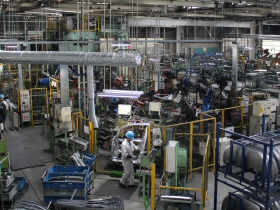
インサイトの現場
- インサイト化はこれで完了ということなのでしょうか。
高田:部品製造のインサイト化についてはここでいったんは完了ですが、今後は遠方サプライヤー様からの納入部品の受入れや、仕訳、ラインサイドへ運搬を行っている物流業者様に水島製作所内へ入って作業をしていただく部品デポ作業のインサイト化など、部品物流改善となる作業への展開を計画しています。
野村:それと、既に導入したインサイトのラインについても、物の配置や動きに工夫の余地がありますから、それもやっていきたいですね。TECO活動のインサイト版みたいに。これはNMKVのコスト低減の別のミッションの中でやっていくことになるかもしれません。とにかく、インサイト化は、メーカー、サプライヤー様双方にメリットのある活動ですから今後も積極的に取り組んでいきますよ。
- 本日はありがとうございました。
2015年5月インタビューより ※掲載の所属、役職はインタビュー当時のものです。