Activities for Closer Production (Same-Premises Production)
Following on from the previous article, this section covers the cost improvement activities at the scenes of production. The key phrase here is “activities to promote same-premises production”. We held a talk session with Yasuhiro Nomura NMKV Vice President / Mizushima Plant Deputy Director, and Naoki Takada and Hiroshi Hayashi from Mitsubishi Motors, and listened to their stories.

▲Takada, Nomura, Hayashi (from left to right)
Activities for same-premises production as part of production restructuring project
- A phrase of “same-premises production” sounds unfamiliar. Tell us more about the phrase.
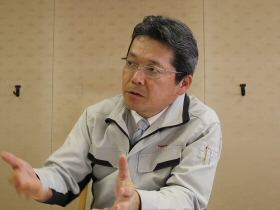
Nomura: I guess it is. It is a phrase we ourselves began to use when we had launched these activities. Probably it sounds unfamiliar to the people outside the industry as well. “Same-premises” means that a supplier is to make components not in its own plant but in the premises of the plant of the manufacturer it sells components to. But the operation responsibility remains only with the supplier while manufacturer’s role is just to provide their premises, a location for production. For your reference, it is called in-house manufacturing if components are made by manufacturers themselves. When the suppliers are offered to make components in the same plant building of car assembly lines of the manufacturers, it is called “same-building production”. If it is done in the same premises, we call it “same-premises production”.
The closer production initiative is a powerful method that reduces logistics costs at the point when components are shipped from suppliers and reduces in-process inventory. It also reduces the risk of deformation, scratches, and contamination that may occur during the transportation process, all of which contributes to the quality improvement as well.
- I see. Was there any activity similar to these in the past?
Nomura:Prior to this collaboration with Nissan, we had been promoting a project of production restructuring at Mizushima Plant. The project encompassed the process to restructure production lines that suited the then-existing conditions deemed appropriate based upon the actual production capacity and volume.
Takada:For example, we had a plan aimed at making components ourselves through the adoption of in-house manufacturing; we reviewed multiple lines used for welding processes and considered reducing the number of lines to optimize the scale and utilizing the unused line space for in-house manufacturing. But just around the time of our consideration, we began the collaboration with Nissan, which introduced us the activities called “same-premises production” through NMKV. Needless to say, the components that our suppliers provide are made based by their high expertise and ample experience. We came to a conclusion that it would be more realistic and ideal as a car manufacturer, instead of sticking to an idea of in-house manufacturing, if we just propose suppliers to come inside Mizushima Plant premises to make components at the minimum logistics costs. From this conclusion, we adopted the idea of “same-premises production” to begin to negotiate about the implementation with five of our suppliers.
Hayashi:Although it was the first time for Mitsubishi to adopt the “same-premises production” idea, we were capable of creating a new scheme by enhancing the concept with our plans for the production restructuring and with ideas and experience of Nissan.
NMKV leadership: fast and optimal implementation
Nomura:In addition to the concept of “same-building/same-premises” approaches, Nissan provided us a list of recommended components for each of same-building / same-premises purposes. Mitsubishi has returned the favor by accelerating the processes at Mizushima Plant focused on production restructuring.
- It sure seems an ideal example of corporate collaboration.
Nomura:That’s right. But I think NMKV’s role is critical here. Usually, any key knowledge or expertise that enables reducing any kind of costs belong to the top confidential secret within any company. It does not come easy. By having an intermediate entity like NMKV, it has become possible for the first time for two companies to share their experience and expertise, which details had not been known until disclosed by the counterpart. As the result, Mizushima Plant is reborn as a lean and highly efficient plant which is truly suitable for producing more of low-cost and high-quality Kei-cars.
- I see. Again, “Picking the best” spirit seems to be the core of the value creation capability of NMKV. Tell us how each of you work in the project in what roles.
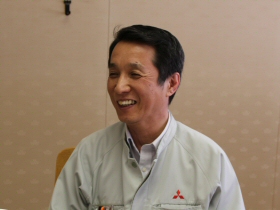
Hayashi:The person in charge of the project of production restructuring at Mizushima Plant is Nomura-san Deputy Director of the plant. Under his supervision, Takada-san and I worked together as a duo to promote the activities.
Takada:We had been formerly working as team members of the production restructuring project. In line with the former task, we have been engaged in the reviewing of implantation plan, making necessary arrangements for actual implementation, and checking the progress, etc., for the activities to promote same-premises production.
Nomura:I assumed a position as an NMKV representative. While I work to coordinate the sharing and gathering of data and expertise from Nissan and NMKV team members, I also serve as Deputy Director of Mizushima Plant to administrate and take control of the entire implementation phases including checking the master plan and taking follow-up actions, with two members here Takada-san and Hayashi-san.
Relocation of production facility: a project called “never-stop”
-So you are the center of activities of same-premises production. Tell about the challenges you encountered during the work you do.
Nomura:First of all, it was hard for us to find suppliers willing to cooperate with the activities of same-premises production. We had to explain from a scratch, starting from what it means by same-premises production. One of the typical responses was “do you mean to make components on your own? Are you buying from us or making them in-house?”. We assured them carefully that “no that is not true. It means that we offer our suppliers a space within our premises to make components. We want you to relocate equipment into Mizushima Plant, where you will be making components for us”.
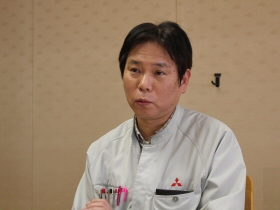
Takada:With the support from the Procurement and Supply department, I began negotiations with our suppliers. An ideal way of doing it was to consult them about same-premises production when we actually build production lines of components for a new vehicle model. Unfortunately, by that time the lines for the existing models, DAYZ/eK Wagon and DAYZ ROOX/eK SPACE, have already started production operations, which meant that we had to relocate the exiting lines. The relocation costs incurred remained as an obstacle. But in the end, we were able to overcome the difficulties of such relocation, thanks to the proactive support and help from the suppliers who kindly understood the positive aspects of same-premises production which led to logistics costs improvement while securing their expertise.
Hayashi:The most difficult part, as expected, was the process of actual relocation. For us, it is the lifeline to maintain the production schedule and to sustain the quality at all costs. By all means, we had to avoid any event of production suspension over the lines due to the quality issues arising out of the relocation process related to the implementation of same-premises-production. For this reason, the available periods for such relocation were only within long holidays such as the Obon festival, or year-end and new year holidays. The welding lines we planned to relocate during the year-end and new year holidays would require a large volume of construction work, so we had agreed beforehand to allocate additional timeframe to re-confirm the quality of items once the relocation was completed. The supplier in charge and ourselves worked together 24 hours a day with two shifts each in daytime and other in nighttime; we relocated the facilities and confirmed the components made were fine-tuned to a level that satisfied the standard. The relocation was successful, and we were back on the regular production flow when the holidays were over.
- It was quite a challenge behind the scenes of relocation to implement same-premises production. I was impressed. What is the outcome of your efforts at this moment?
Hayashi:At the last cycle, we have targeted five suppliers which handled welding assembly, glass assembly, underfloor bent-plumbing components; these components had been already in production by suppliers, thus deemed to have benefits from same-premises production than the relocation costs - because such components were big in size, packaging or packing being inefficient, and high in logistics costs.For example, take a look at the welded assembly components such as engine foods, doors, etc. In the past, the shell plating parts used for the foregoing were first pressed at Mizushima Plant, then transported to the supplier's site for welding and assembling followed by transporting back to Mizushima Plant again; it was a logistics process upside down. By the implementation of same-premises-production, we could eliminate the waste in logistics process and improve the quality of shell plating parts. I believe this is indeed a critical improvement which will continue to be effective for any different future vehicle models.
Next steps for same-premises-production
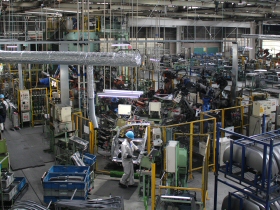
A scene from same-premises-production
- You have reached a big milestone for same-premises-production?
Takada:We have completed the same-premises-production phase for the production of components for the time being. In the future, we plan to expand the activities onto the operations that have direct impacts on the improvement on logistics of components, such as the acceptance of components delivered from physically distant suppliers, or the acceptance of logistics partners whose duty is to deliver items to the assembly lines so that they can set up a small warehouse for storing components (a “depot”) in the same premises of Mizushima Plant to do their logistics operations, etc.
Nomura:Additionally, I think there is still room for improvement in the lines where we have already implemented same-premises production from an aspect of effective placement or movement of items. I would like to do that as well. It may turn out to be a variant of TECO-oriented activities. It may be included in one of another cost-saving missions that NMKV pursues. In any case, I'm pretty sure that the same-premises production initiative is an activity that benefits both car manufacturers and suppliers. We will continue to work proactively toward the targets we set.
- Thank you for your time.
The talk session was held in May 2015. The positions they assume and affiliation they take in this article are as of at the time of the session.