Logistics Cost Reduction Activities for Automobile Components
This section introduces our cost reduction activities in the area of logistics of automobile components. NMKV has been playing a leading role behind this initiative involving Nissan Motor, Mitsubishi Motors, and their logistics partners, which goes beyond the Kei-cars boundary from a broader perspective that encompasses the entire flow of logistics of automobile components.
We had a talk session with Kazuhiko Kaneko (Mitsubishi affiliation) Leader, Hironao Shiraga (Mitsubishi affiliation) Manager, and Itsuki Kojima (Nissan affiliation) Manager, all belong to NMKV Logistics Project Group which serves as the main driver for these activities, and listened to their stories.

▲Shiraga, Kaneko, and Kojima (from left to right)
Each member having a different strength
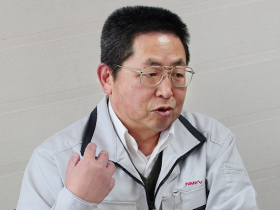
- Tell us about your logistics cost reduction activities for automobile components.
Kaneko:Similar to TECO activities, the base idea is taken from the activities in the Mizushima Challenge. In the case of Mitsubishi, which serves as a production base for NMKV vehicles, the logistics had been optimized within each plant on a unit of components basis. This new activity aims to reduce costs by applying the Nissan methods to achieve entire process optimization. We work in NMKV Logistics Project Group that is responsible in administering these activities.
- Tell us about your work experience, and what kind of role you take
Kaneko:Kojima-san works at Nissan whose task is to improve logistics operations, he is an expert of logistics of automobile components. Shiraga-san is an expert of manufacturing/production who knows everything what’s happening inside the plants. As for me, I am an expert of encouragement whose task is to say, “do your best!” to these two, while taking part in the logistic management activities.。
Kojima:I have been working to reduce logistics costs through my involvement to Nissan’s TdC (Total Delivered Cost; total cost reduction by vehicle type) Challenge. The method Nissan adopted was to review logistics spending from a bird eye view, make necessary adjustments across different departments, and lower the costs as a whole. At NMKV, we put efforts into establishing a “logistics method unique to NMKV”, based on the way of thinking and methods which I have learnt from the aforementioned activities.
Shiraga:I have been engaged in manufacturing and production all the time. Which can be interpreted that I have been a customer from the view of logistics operations, so to speak. I’m making full use of my experience as a customer for this cost reduction project. There are many new discoveries from the perspective of a team member in the project to review processes which have benefitted me as a customer. I think such discoveries serve well in my current post, and I can learn a lot from such experience.
- Tell us about the strength you have as a team.
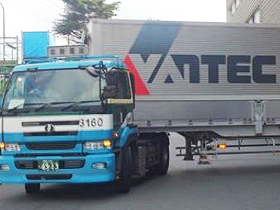
Shiraga:Three of us have already reached an agreement that we should “take advantage of what’s good about Mitsubishi and adopt the methods of Nissan”, so we began with visiting the scenes of logistics operations above all; we did surveys, collected data, conduct present data analysis, had discussions aimed at cost improvements, and put our plans into action. The days passed while we repeated the flow above.
Kaneko:There is a unique culture and atmosphere among the staff working in the plants and they have strong pride in their jobs. Think of an outsider stepping in their plant out of nowhere and saying, “your way of work isn’t efficient enough”, it won’t work. They would never agree. Therefore, the most important thing is to understand what’s really happening in the operations. To do this, we decided to begin our work with the awareness penetration by Shirakami-san who knew well of what’s happening in the plants, while referring to the expertise and knowledge of Kojima-san. Because all three have different strength, I think we served well as a team.
Building win-win relationship with logistics partners
- Tell us about your achievement so far.
Kaneko:We have achieved the initial reduction target. One of the purposes of this activity is to share the outcome with the logistics partners and to build a win-win relationship with them, and it has been successful as well. The logistics spending of automobile components is large in quantity and the operation runs throughout the year in a stable manner. For that reason, the outcome of efficiency improvement can be huge for those logistics partners as well.
Kojima:Many tend to deem logistics as a simple task. On the contrary, it is a complex set of operations which involve dozens of people and companies. Which naturally means that the points of improvement vary, from the routes of transport, packaging and packing style, to transportation methods. It would be quite difficult for a single logistics company alone to plan and implement across the points above, not to mention to improve the efficiency across the board. Our proposal for those partners is that to form a team with all parties including ourselves to think what we can do for such improvement and also to share the benefits generated therefrom. I think it serves as a worthy reason for logistics partners to join.
Wearing two hats and power of teamwork
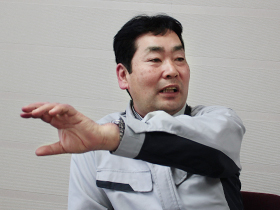
- You work well as a team. But I understand that all of you work at different branches?
Kaneko: I work at Okazaki, Shiraga at Mizushima, and Kojima at Atsugi. Not in the same location at all. As I work for my parent company concurrently, I have two days a week for this activity. In these two days, all of us gather at locations such as plants, meeting rooms etc., to have intensive discussions on the activity. We have tried a telephone conference style to save costs and time, but it turned out to be a terrible try.
We did it only once. Now we are back to the conventional meeting style.
Shiraga:You should listen to Kojima-san’s story about wearing two hats, it’s pretty interesting.
Kojima:Not really into the story of wearing two hats…to be honest, it’s pretty tough. I’m barely doing my job, always trying to find any efficient trick I can use of, such as doing tasks in my spare commuting time in the bullet trains. But after all, I think I’m blessed with colleagues. Staff of the plants support my work, and my boss understands what’s I’m working on. My team members are developing their capabilities. The project here in NMKV is a rare and great opportunity you can’t have if you just stay in Nissan. No matter how hard it is, I want to complete the task I was assigned to. And there are still a lot that I want to put my hands on.
Establish a logistics method unique to NMKV
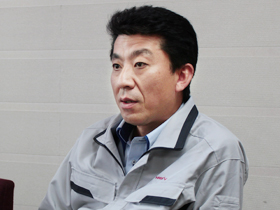
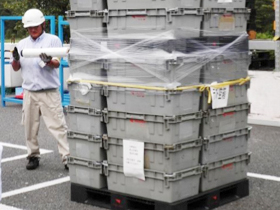
- Lastly, what is the thing you want to do most?
Shiraga:From the beginning, we all agreed that we would do what only NMKV could do. The thing is to launch a “joint delivery” system, which we have already begun working on. This idea was proposed by Kojima-san, wasn’t it?
Kojima:The joint delivery system aims to transport automobile components of two companies in the same cargo between two production bases of Nissan and Mitsubishi. This is a revolutionary initiative that only NMKV can tackle. The drawback of this idea was that no one has ever tried such a thing and we had no way to follow the precedent. We were clueless where to begin. So, we gave it a try anyway. And after learning from many problems and issues, our idea began to take shape. It took four months for the launch, and I know there would be a lot of hardship in the days to come. But we’re determined that we will keep nurturing the idea carefully so that it would lead us to greater outcome.
Kaneko:The more we dig deep, the more challenges we face. There are heaps of tasks on the list, but we’re looking forward to each one of them. The past projects we had finished only served as a set of catalysts, so to speak. If we quit now, things will go back to where they used to be. Our activities must not be just a skyrocket shot for once. The challenge from now on is to think how to build solid grounds for them to grow.
- Thank you for your time.
The talk session was held in January 2015. The positions they assume and affiliation they take in this article are as of at the time of the session.