TECO Activities
NMKV is a company focused on the product planning and development of Kei-cars. Concurrently, NMKV serves as a facilitator between two parent companies for the purpose of creating synergy throughout both their businesses.
In this section, we introduce our “TECO (Total Effort for Cost Optimization) activities, a cost improvement initiative undertaken mainly by Mizushima Plant of Mitsubishi Motors. The Mizushima Plant is the production base for cars which are planned, developed, and produced by NMKV. We had a talk session with Shinzo Nomura (Mitsubishi affiliation) Director (as of March 2014) and Isao Kasama (Nissan affiliation) General Manager, both belong to NMKV Vehicle Function Group which is a promotional department for TECO activities and listened to their stories on how they take their part in promoting “TECO activities”.

▲Nomura and Kasama (from left to right)
TECO activities: joint initiative with suppliers
- I heard that TECO is an activity that has been named by Nomura-san.
Firstly, tell us about what you do in TECO activities.
Nomura:At the Mizushima Plant of Mitsubishi, efforts have been made to improve the productivity and in streamlining business operations, through the initiative called “Mizushima Challenge”.
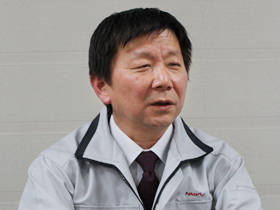
Among these activities, there is a particular set of activities that refer to the cost reduction of the materials used by NMKV planned/developed vehicles, and I named it “TECO” activities. TECO stands for “Total Effort for Cost Optimization”, and the idea behind it is to call for action to “use all resources and focus on the optimization of material costs”. Originally, there was another cost improvement initiative carried out in Mitsubishi called “SWS” (Supplier Workshop). I have reactivated this initiative by adopting the “THaNKS” methods utilized by Kasama-san and his team members in Nissan and then used them to develop and enhance TECO activities. At NMKV we call it a “NMKV model”, whose strategy is to “pick the best” of two companies to gain a little something extra. TECO is an excellent example of such model.
Kasama:“Using all recourses” includes not only Nissan, Mitsubishi, or NMKV but also our supplying partners. 70 percent of automobile production costs are associated with purchase of components and materials.This the right place to get started. There is a significant possibility for improvement, even more so if we can cooperate with our suppliers. In the fiscal year 2013 we decided to make a first attempt for NMKV developed vehicles. We selected several suppliers and began to act together for the purpose of TECO. By the way, the activities of TECO which focus on reduction of components costs encompass not only the first-tier supplier but also second- and third-tier suppliers. We are taking a deep dive into the matters anything related to cost improvement, so to speak.
Nomura:The key to these activities is that all parties, the suppliers, Mitsubishi, and NMKV, work together to put efforts for the purpose on an equal footing, with the support from Nisan. And that all parties think hard to solve issues and strive to find solutions. And that, fruitful outcome obtained from these activities is to be shared by all parties on a fifty-fifty basis. Such policy of these activities was also supported by our suppliers. It went very smoothly thereafter.
- Tell us about the flow of typical TECO activities.
Nomura:TECO activities take about six months from the preparation phase to the final closing phase. The principle of TECO is to scrutinize what’s happening in the actual scenes of production. After notifying our suppliers by visiting them and reaching mutual understanding in advance, we then hold a set of special sessions for cost improvement for four consecutive days. Issues or challenges identified through such discussions are to be resolved by specific follow-up meetings thereafter.
- How was the response from your suppliers?
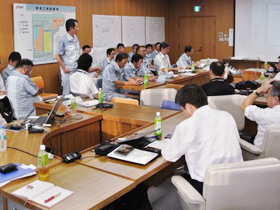
▲A scene from TECO session
Nomura: I didn’t feel a sense of resistance among them. But at first there were voices of concern and uneasiness about what kind of activities they were to be involved. In the conventional activities held before TECO, most meetings and sessions were shorter where a few members visiting suppliers’ sites by a day trip, which participants were of a single department not multiple at a time. But in TECO, when there are many, I recall that up to 25 members who were in charge of respective production processes visiting the supplier’s site just for a preparatory meeting. In return, there were the same 25 attendants from the supplier side.There was total 50 members working for the activity. It was a spectacular scene. I now think that the supplier must have felt “this is not what we think we knew”.
Kasama: Intensive actions for improvement are not something we can one-sidedly demand our suppliers to take. Together with suppliers, we scrutinize every aspects of production to find for any inefficiency left out for improvement. We offer analytical methods and share tips for improvement, all of which will be the base for discussions between suppliers and ourselves to reach the best solution adoptable for such improvement – our idea has been accepted by the suppliers unreluctantly. As Nissan’s THaNKS activities have provided us a variety of benchmark formats and convenient tools for cost improvement processes, it was easier for us to visualize and measure improvement indicators through utilization of such tools.
Nomura:As a promotor I was all there looking how it progressed. It was truly an exciting activity to watch.
Big results from four-days intensive sessions
- You were pretty sure it would go well?
Nomura:Yes. The outcome that followed proved my confidence. We were able to achieve target values in almost all areas of production. As for the areas remained under the target values, they also improved to the level very close to such values. To tell the truth, I personally felt that the target values that had been set were a little too high. I was surprised by the result and was very happy. Allegedly, the suppliers thought highly of such result as well.
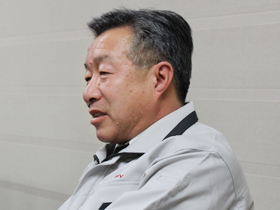
Kasama:There were many possibilities, a dozen hundreds of them, for improvement we found in the activities: from a short-term improvement idea such as a slight change in the workflow or making a slight location change of pallets that carry components to a long-term improvement idea including redesigning of components that takes several months, etc. Because we materialize such ideas in daily operations, the result becomes obvious for everyone on a daily basis.
Nomura:From an aspect of logistics, what a car manufacturer sees every day is a set of components as a set of delivered boxes neatly packed. In TECO activities, we draw a big diagram on a large sheet of paper which describes the entire supply chain including sub-components. Although it took time and efforts, there was a time when we found a set of sub-components were unnecessarily transported from east to west and vice versa, which involved additional loading/unloading processes and extra resources. So, it provides us many ideas for further rationalization. Each of such issues may look trifle, but we are still reviewing each of them if there is any room for improvement.
Kasama:When we live under the same roof for four days, we can expect to hear the real and honest opinions about the issues they face in the scenes of supplier’s site. In response to their concern, we naturally offer a helping hand saying “we have a specialist in the field of your problem. Could I bring this specialist for the next session?”. The sessions had been effective in deepening mutual understanding and trust.
NMKV driven TECO activities
- What is the role of NMKV in TECO activities?
Nomura:I and Kasama-san’s roles are to serve as a promoter and facilitator of TECO activities. We create a master plan. We collect the results of activities and analyze them.
Kasama:If Nissan and Mitsubishi had not cooperated to form a unique company called NMKV, TECO activities themselves would have been impossible in the first place. That’s all I can say.
-Lastly, tell us about the future of TECO activities.
Nomura:In the fiscal year 2013, we have learnt from the trial phase that the activities of TECO were indeed very effective for improvement. So, we will expand the list of target suppliers from the fiscal year 2014 and beyond.
- Thank you for your time.
The talk session was held in May 2014. The positions they assume and affiliation they take in this article are as of at the time of the session.