Physical phase: smooth communication is a key to success
When the digital phase is completed, the physical phase kicks off– a phase of conventional automotive manufacturing. The process begins with the trail production using the final version of mold components; each of production lots is tested to verify its performance and quality. The final production lot will be used to confirm if it satisfies the quality standard for mass production. The objective of the physical phase is to confirm and obtain factual evidence for the serviceability of components which naturally remains unknown until they are actually made – although there were a various kind of testing conducted already in the previous digital phase. Each production lot has a specific goal which details are defined by the KPI. In this phase, they solve any problem in real time that may arise from the manufacturing process which methods are confirmed and coordinated in line with the actual scenes of production, not to mention the verification process of the level of performance and quality; all of which will lead to the KPI targets.
Under this new Scheme, the physical phase of product development succeeded beyond everyone’s wildest expectation. Saito CVE (Chief Vehicle Engineer) explains the reason that “it was successful thanks to the team members of two companies who gathered under the same roof and kept communication smooth and straightforward among all”. Nissan, which had no experience of Kei-car product development, faces a variety of challenges including a smallness of components in comparison with regular passenger vehicles. There are other major challenges as well, which fact urged Nissan to have intensive communication with the Mitsubishi mechanical designers, the experts in Kei-cars projects. By preparing an umbrella named NMKV where the members of two parties can gather, they have overcome the challenges through intensive communication beyond the corporate barriers.
Of course, there was no simple road to success. As the members of two companies belonged to separate organizations whose workflows are different to each other, it became inevitable some tasks were omitted or skipped throughout the entire patchwork of processes. As a countermeasure, they faithfully made and complied to detailed rules, such as “the order placements for the components to be supplied by Nissan for a Nissan-designed vehicle are the responsibility of Mizushima Plant”. As there were a dozen of such purchasing combinations, they started by setting up purchase categories for each set of specific items. As the result, there was not a single missing component confirmed in the first prototype model assembled at stationary spot. It was truly an outstanding achievement even from their time-tested experience.
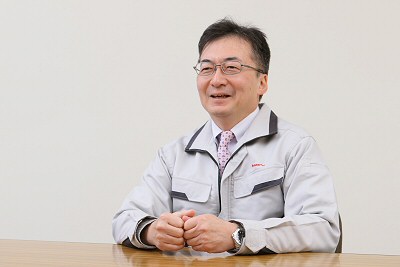
Saitou, CVE
“Our goal is our customers. A great vehicle makes its beholder happy. My single-minded dedication to the automobile development is underpinned by my strong belief. And there is no greater satisfaction than the joy when our car products are highly evaluated by our customers. We are quite confident the next model deserves such accolade”, declares Saito CVE. The model’s particular design elegantly manifests both companies' signature Brand identities. The planned machine performance is already competitive enough against the rivals’ models. The last task remained is to fine-tune the product to perfection to drive the satisfaction of the customers that await in the market.