4. 生産
水島製作所に約80億円の投資
三菱自動車工業は、新型の軽電気自動車(EV)を生産する岡山県倉敷市にある水島製作所に、日産自働車と共に約80億円の投資をすると2020年7月28日に発表した。
水島製作所は、1943年(昭和18年)に操業をはじめ、軽自動車や小型車、商用車の生産を行い、世界初の量産EVである三菱i‐MiEVの生産を2009年から行ってきた。また、車体組み立て工場だけでなく、エンジン工場、鋳物・鍛造工場、バッテリーパック組み立て工場など、自動車製造にかかわる一貫した生産能力を持つ世界有数の製作所でもある。
そこへ新たに投資された約80億円は、どのように役立てられたのか。
「新型軽EVの組み立ては、エンジン車と同じ生産ラインで行うため、EV生産にも適合する投資が中心になります」と、NMKVで最高生産技術責任者(CPEO:Chief Production Engineering Officer)を務める古谷公一は説明する。
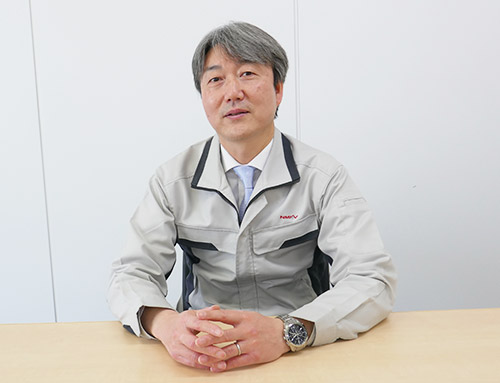
古谷 CPEO
「具体的には、新型軽EVでは電動化に伴いコンポーネント関係の部品が新しくなり、車体も新しくなります。そして、コスト競争力を高めるため、三菱i‐MiEVでは購入品であったバッテリーケースを内製化しているので、そのプレス加工や、溶接、塗装などの設備投資が必要でした。またバッテリーがこれまでのi‐MiEV用と異なり日産リーフで使われているものに替わるので、組み立てや検査の設備も新しくなります。モーターの動力をタイヤへ伝える減速機は、アウトランダーPHEVでも使っておりますが、新型軽EV搭載に伴う生産ラインの改造が必要です。それから、i‐MiEVと新型軽EVではパッケージングが異なりますから、組み立ての際にエンジン車と違う部品を搭載する上での対応も変わります。この投資も新型軽EVのためです」
一方で、これまでのi‐MiEV生産でも、エンジン車と製造ラインの混流は行っており、その経験があることから、今回、設備投資は抑制できたと付け加える。
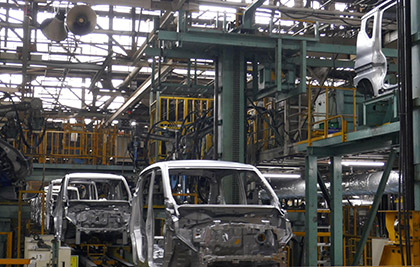
製造ライン
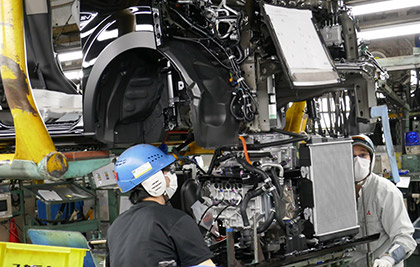
モーター車載工程
軽自動車のEVを製造するための工夫
水島工場では、どのように新型軽EVを製造するのか。エンジン車と同じ製造ラインで生産するには、部品点数の違いや、電気部品特有の取り付け方法を考慮しながら段取り、作業工程数や作業時間に差が生じない工夫が必要になる。
「製造ラインの様子を模式図で表した」というのは、生産プロジェクトグループの平井泰忠ジェネラルマネージャーである。(図1を参照)
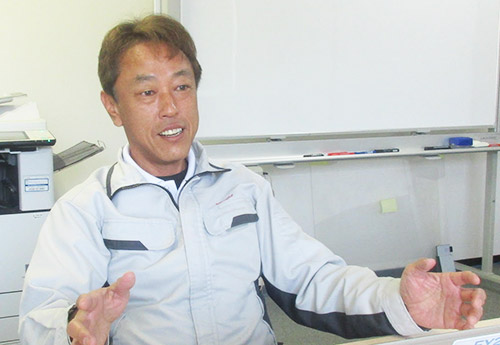
平井 ジェネラルマネージャー
新型軽EVは、エンジン車と同じ様に、模式図1の左から右へ組み立て作業を進めていく。
「エンジン車と相対する部品として、左から、燃料タンクに対してバッテリー、エンジン駆動系に対してはモーター駆動系、排気マフラーに対して充電ケーブルという具合に、生産の流れを考えることができます。こうすることにより、生産工程や生産時間にエンジン車と新型軽EVで差の出にくい手順にすることができます。ただし、微調整は必要です。たとえば、マフラーと充電ケーブルでは、部品の形態や固定の仕方に違いがあります。マフラーは金属の配管ですが、充電ケーブルは配線であるため柔らかく、固定するために止める箇所も数多くなります。そこで、製造ライン左側の燃料タンクの工程を活用することにより、配線を止める作業を二工程に分け、手数や工程時間に差が出にくいようにしました。また、バッテリーは大きくて重いため、右端のマフラー工程の段階で床下に車載し、ここでも充電ケーブルの充電口側の配線を行います」
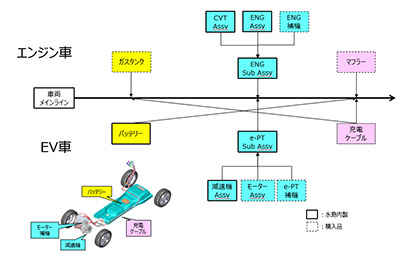
図1:コンポーネント違いの生産ライン対応
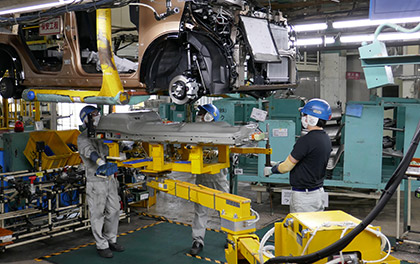
バッテリー車載工程
日産自動車で生産の仕事に永く携わってきた平井にとって、今回の新型軽EVのバッテリー車載について、i‐MiEVの生産をしてきた三菱ならではの工夫を知ることになった。
「日産は重いバッテリーの車載を自動化していますが、軽自動車は原価を抑え、手ごろな価格で買えるEVにすることも重要なため、圧縮空気を利用し人の作業で車載できる仕組みを三菱の人たちは考えていました」と話す。
ほかに、騒音と振動への対策が、新型軽EV製造のうえで重要な課題であったという。
「減速機は、通常、軸に歯車を圧入して製造しますが、この段取りだと軸の精度に加え、歯車の圧入精度も重なり、軸に対し歯車が若干斜めになってしまう懸念があります。すると歯車の噛み合いにズレが生じ、それが騒音や振動の原因になりやすいのです。軽自動車のようなサイズに制約がある小さな車両では、それらの振動や騒音が耳に届きやすくなるため、新型軽EVでは軸に歯車を圧入してから加工する段取りに替えました。そうすることで、加工精度に注意を払えば、歯車の噛み合わせに狂いが出にくくなります。この作業変更によって、新型軽EVは試作の段階から減速機からの騒音や振動の問題は起こらず、順調に量産へつなげることができました」
軽EVならではの原価を踏まえた改善は、ほかにもある。古谷CPEOは、
「バッテリーケースを、i‐MiEVは樹脂製であったのを、新型軽EVでは日産リーフと同じ板金製としたことで、水島製作所にて内製できました。バッテリーケースのような大きな部品を外注すれば、輸送費だけでも大きな負担になります」と、説明する。
品質向上へ向けた取り組み
製造上の苦労は、生産ラインの工夫以外にもある。生産プロジェクトグループの小暮尚志マネージャーは、
「新型軽EVの床下構造は、日産車と三菱車で同じですが、客室などがある車体側には商品性の違いによる仕様の異なる部分があります。内外装部品の違いがほとんどですが、その対処が製造ラインの工程で鍵となりました。仕様違いによる取り付け間違いを起こさないように、部品に識別を付けたり、ランプによって作業指示を出したりしています。この点は、エンジン車の日産デイズや三菱eKワゴンの製造も同じなので、これまでの経験を活かしています。さらに、開発の部署と協力し、部品の見栄えが異なる場合でも、取り付けボルトの本数を同じにするとか、取り付け方法を同じ手順にするなど、間違いを起こさない作業で製造できる工夫を入れ込んでもらっています」と、NMKVとしてエンジン車製造で積み上げてきた経験を基に、開発部署と協力しながら、生産ラインでの作業や製造時間に差の出ない工夫を織り込んだと話す。
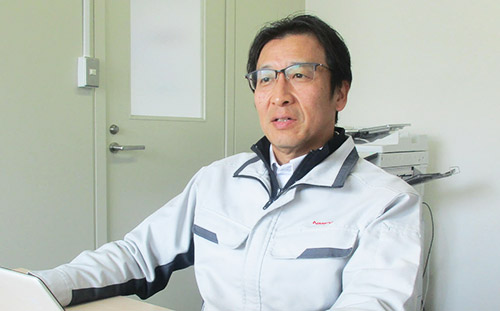
小暮マネージャー
EVならではの工夫では、生産プロジェクトグループの樋口貴博マネージャーが次の点を指摘する。
「エンジン車に比べ、高電圧の配線が多くなりますので注意が必要です。しかし水島製作所はこれまでi‐MiEVを製造してきた経験がありますので、絶縁対策などは実績があります。組み立てに際して間違いが起こらないようにするには、小暮もいいましたが、開発の段階で組み立てミスを発生させない設計をしてもらうように協力してもらいました。その際、コンピュータによるデジタルモデルを利用して作業手順を検証し、開発者と我々が一緒に懸念される点を指摘しあって改善しました」
そのうえで、作業工程ごとの点検も適切に行うことにより、間違った組付けの防止を行っている。樋口マネージャーは、
「工程監査を専門に行う部署があり、検査の様子を確認してもらいました。三菱自動車は、ドイツのダイムラー社と提携していた時代にクォリティチェックゲートと呼ぶ方式を採用し、現在は三菱モータース・デベロップメント・システム(MMDS)として継承しています。同時に、NMKVは日産との合弁事業ですので、日産のマネージメントシステムに沿った工程検査にも従っています。新型軽EVでは新たにバッテリーケースを内製していますので、その気密性や、充電に関わる検査が追加となり、この部分は冒頭に古谷が紹介した約80億円の投資の一部となっています」
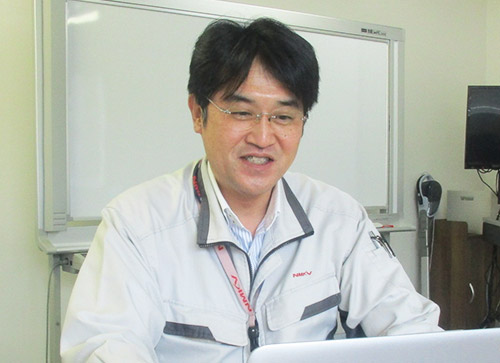
樋口マネージャー
古谷CPEOは、確実な製品の仕上がりとするため次のような手法も採り入れていると補足する。
「作業工程ごとの品質確認では、作業班ごとのゲートカメラや工程毎の作業観察カメラを設置し、不具合の早期発見、対策を実施できるようにしています。このように各工程で節目を設けることで、お客様に間違いのない品質のEVをお届けできるようにしています」
過去10年を超えるEV生産がもたらす裏付け
これまでも事例が出たが、水島製作所は2009年に発売したi‐MiEVを通じ軽EVの製造を行ってきたことにより、新型軽EVの生産において10年を超える経験が活きている。このため、古谷CPEOは、
「車両パッケージングにおいて、i‐MiEVはリアモーター・後輪駆動で、新型軽EVはフロントモーター・前輪駆動となりますが、駆動用バッテリーは車体中央の床下搭載のため共通性があり、i‐MiEVを生産した製造ラインの活用に大きな支障はありませんでした」と、語る。
品質保持では、商品生産化プロジェクトの柏原一典プロジェクトマネージャーが、
「バッテリーの取り扱い、搭載方法、充電検査など、安全や品質に関わる懸念材料はあらかじめ設計段階でi-MiEVの反省を織り込むことができているので、試作の段階から量産に近い品質を実現することができました」と、自信をのぞかせる。
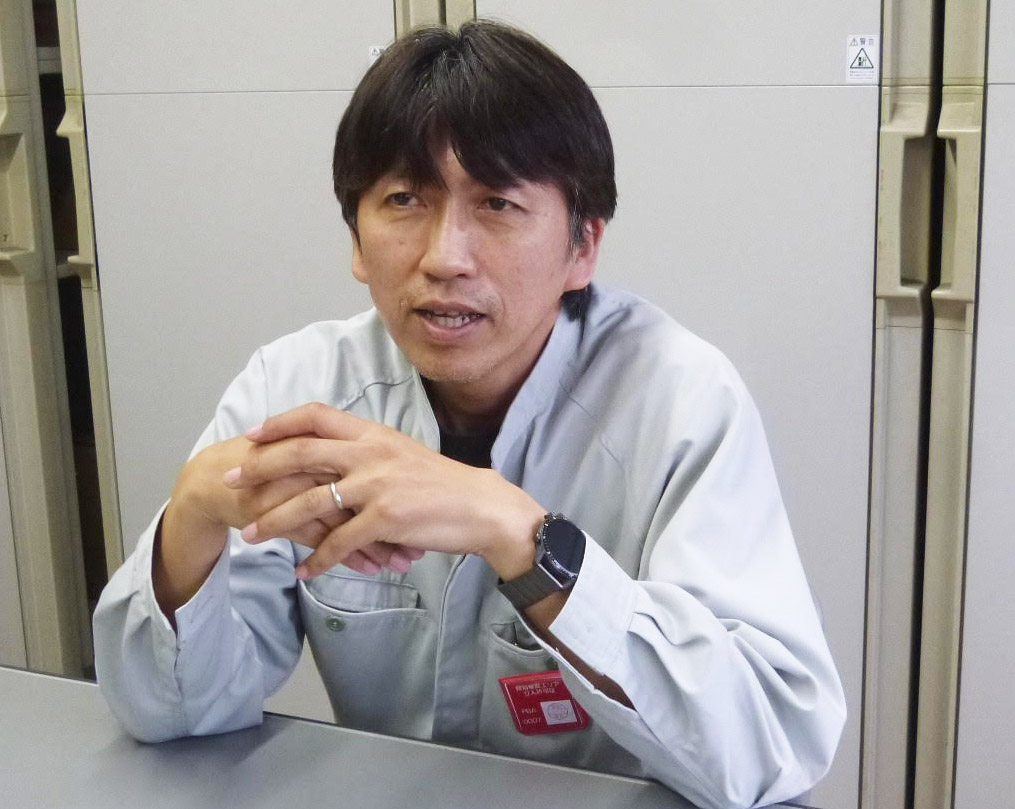
柏原プロジェクトマネージャー
一方、i‐MiEVとは異なる新たな取り組みもあった。商品生産化プロジェクトの荻野学担当マネージャーは、
「部品としてのリチウムイオンバッテリーは、i‐MiEVのときと違い日産リーフで使われているラミネート型となったため、水島製作所にとっては初めての経験になります。そこで、日産へ見学に行かせてもらい、追浜工場の現場で意見交換しながら生産の要点を教えてもらいました。通常、競合メーカーの工場内部へ入ることはできないですが、日産と三菱の提携関係により、細部にわたり立ち入らせてもらい学べたことは貴重でした。充電検査も、中身のバッテリーが日産のラミネート型であるため、日産の経験や知識を活かし、それを三菱に導入できた点は大きいです」と、国内で永年にわたりEVの開発と生産を続けてきた日産と三菱ならではの成果を印象深く話すのである。
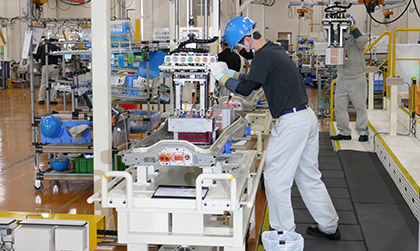
バッテリー組立
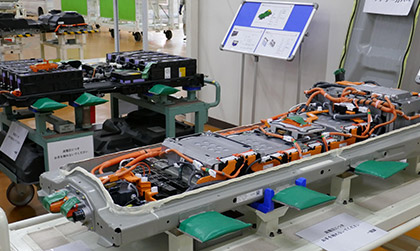
新旧バッテリー比較(手前が新型、奥が旧型)
新型軽EVとして新たな点は、バッテリーの冷却の仕方にもあると荻野担当マネージャーはいう。
「i‐MiEVは空冷でしたが、新型軽EVは液体冷却となり、空調の冷媒を使っています。開発部署に関わる話ですが、冷媒の漏れが起きないようにすることも日産の経験を活かしています」
そのほか、充電口にも新たな試みがある。
「i‐MiEVは、エンジン車の給油口を活用したうえで、200ボルト(V)の普通充電と、CHAdeMO(チャデモ)の急速充電で、充電口を車体の左右に分けていました。新型軽EVは、運転席から降りて充電しやすいように、車体右側に普通充電と急速充電の口を両方設置しています。軽自動車の小さな車体の片側に二つの充電口を設けるには工夫が必要ですが、開発と生産で一緒に工夫した点といえます」
日産と三菱の提携がもたらした利点
NMKV(日産・三菱・軽・ヴィークル)は、2011年に日産と三菱が設立した軽自動車専門の合弁会社だ。歴史も風土も異なる二つの自動車メーカーによる合弁事業の利点はどこにあるのか。
荻野担当マネージャーは、次のように語る。
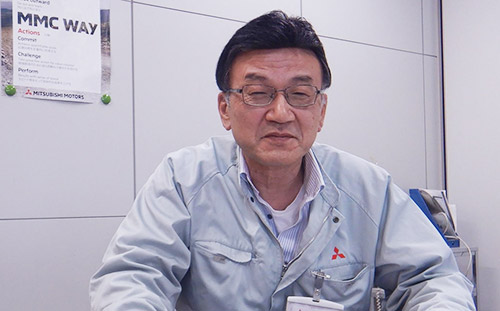
荻野担当マネージャー
「図面を形にするのが生産の仕事です。それに際し、必ずしも図面にすべてが描かれているわけではなく、現実の物づくりでどう対応するかが現場の能力です。一例は、今回採用した内製のバッテリーケースについて、上下二分割のケースの気密性をどう保つか。日産リーフが使ってきたラミネート型バッテリーを三菱は使ったことがないわけですから、何に注意を払うべきか。そうした要点について、日産の現場で仕事をしてきた人たちの生の声を聞くことができたのは大きいです。EVを製造するうえで、全体的な物づくりには共通性があり、日産と三菱の違いはさほど大きくありません。しかし細部の現場対応という点で、生産技術を担う者同士が両社の経験を基に一緒に話せた点は合弁会社のよさといえるでしょう」
約80億円にのぼる投資を含め、新型軽EVの生産をはじめるにあたり、水島製作所はどのような活気を帯びているのか。柏原プロジェクトマネージャーは、次のように様子を語る。
「軽自動車は水島製作所の主力であり、i‐MiEV誕生のときからEVを製造してきた経緯もありますから、新型軽EVを生産する現場は非常に機運が盛り上がっています。脱二酸化炭素への期待がさらに高まるなか、軽EVに対する需要は増していくはずです。それによって水島製作所への注目も集まるのではないでしょうか。お客様に喜んでいただけるよいEVを作るのだという思いが高まっています。
あわせて、これから先のEV需要増加に備え、EV専用工程の能力増強や、EVを生産する製作所としての脱二酸化炭素への取り組みについて、日産を参考にしながら将来への施策を検討していきます。設備を刷新する機会をとらえ、省エネルギー機器を導入するなど具体像を明らかにしながら、実施時期を明示していくようにします。
水島製作所は、i‐MiEVやアウトランダーPHEVなどの電動車両で通勤する社員も多く、駐車場には充電設備が整っています。新型軽EVは、駐車支援や運転支援の機能も備わり、EVというだけでない魅力もありますので、社員だけでなくその家族の関心や、購入意欲も高まっています。水島製作所内の調査では、社員の96%が新型軽EVに興味があると回答しています」
生産する人自身が欲しくなる、それが新型軽EVである。
新型軽EVへの思い
新型軽EVへの個人的な思いを各人が語る。
古谷公一CPEO
「2年前から新型軽EVの準備を担当しましたが、丁度、新型コロナ感染拡大と重なり、準備を止めざるを得ない状況もありましたので、色々な意味で今回は生みの苦しみを味わいました。同時にまた、世の中のEVへの機運が高まりつつあり、生産にたどり着けたことは感無量です。日産と三菱の英知が融合した素晴らしい軽EVになっていますので、多くのお客様に乗っていただき、EVの楽しさや喜びを体感していただきたいと願っています」
平井泰忠 生産プロジェクトグループ ジェネラルマネージャー
「品質を含めよい軽EVに仕上がったと自負しています。日本市場を一変させると確信しているので、水島製作所で製造した新型軽EVが、この岡山から拡散し、女性や高齢の方を含め日常的に利用してもらうと、必ずよさをわかっていただけると思います。ことに地方都市で有効な移動手段になるはずで、水島製作所で作り上げた新型軽EVで世界を一変させたいと思います」
小暮尚志 生産プロジェクトグループ マネージャー
「何かを突破するような開発に関われる機会は多くありませんが、心躍らせながら携われる仕事が今回できました。この嬉しさを、お客様にも感じていただけるEVになっていると思います。そうなるように頑張り続けてきました」
樋口貴博 生産プロジェクトグループ マネージャー
「日産と三菱の提携により、三菱にとって久しぶりの新型軽EVに携わることができ、大変ありがたいと思っています。市場を一変させるEVだと思っていますし、そうなることは間違いないと確信しています。量産がはじまるまで気を抜くことなく、お客様に最良の軽EVをお届けしたい」
柏原一典 商品生産化プロジェクト プロジェクトマネージャー
「1年前はまだ品質が狙い通りでなく、期日までに達成できるか不安もありましたが、そこから集中的かつ迅速な対応によって目標達成に至りました。一丸となった取り組みが困難を乗り越えさせ、量産開始に漕ぎつけました。これからもその一丸の取り組みで量産していきたいと思います」
荻野学 商品生産化プロジェクト 担当マネージャー
「i‐MiEVは、なかなか次へつながらず苦しい時代を経てきました。しかしいよいよ新型軽EVが発売となり、感慨深いものがあります。やっと新しいEVが、かたちになった嬉しさを噛みしめています」